During the last weeks we have been researching on how to improve the process of making vias through-hole with TwinTeeth.
There are several commercial products for making PCB vias at home. Some based on small rivets, others on conductive epoxy. You can also use electroplating, which is the method used at the industry. In addition you can use the traditional system which consists of introducing a small wire in each via, solder it at both sides of the PCB, and cut it. For example, if you have 100 vias in your PCB, you have to solder 200 times. This can be time-consuming, but is also boring, absurd, produce a melancholic state of mind and is prone to failures.
None of these methods convince us, and we are sure that there is an alternative way for making vias at home with the help of a robot like TwinTeeth.
Main problem when looking for an alternative method for soldering or electroplating vias is the conductivity of the material. For that reason silver in frequently used in the compounds, but at a cost. Graphene seems coming to replace silver but at the moment of writing this article it is not cheap.
We started researching on it and on how to make conductive ink with graphene oxide but the price of the samples were too expensive for our taste. The idea is to make ink or conductive paste for filling the vias, andif we are going to make conductive ink, we could paint circuits as well, which is the second goal of this project.
We firmly believe in additives methods to make circuits at home and also make them in 3D. It seems that at this stage of technological development we should already have something at the DIY level, but it is not so obvious.
Behind the graphene story and exorbitant prices, we turn to the silver which is the following actor in the conductivity list. Latest researching on reactive silver inks is promising and seems to give good results. Most are based on this paper: "Reactive Silver Inks for Patterning High-Conductivity Features at Mild Temperatures" - S. Brett Walker and Jennifer A. Lewis
Here you can see a video about how to brew it at home: "Make conductive silver ink".
It does not seem complicate, although the silver nitrate needed to make the acetate cost about €50 per 25 grams and probably we will obtain only a few ml after the process. Despite it is quite reactive, it still requires an 85-100°C annealing. In other words: it does not cure at room temperature.
However there are some start-ups that found similar formulations that cure at room temperature and are manufacturing and selling them and also markers. For example this one: http://www.electroninks.com/.
We could use these silver-ink markers on Twinteeth very easily. It is so simple as installing one on the Plotting Toolhead and paint the circuits with it.
Returning to the via topic, in the ranking of conductivity and behind silver we only found copper, so we focus our researching on this material and how to make ink or paste using copper nanoparticles.
Searching on the internet we found some videos of Robert Murray-Smith and his experiments with conductive ink. It has many and instructional videos about how to make conductive ink of different types. The most interesting for us was this one: Homemade copper conductive paint / ink. You can see at the video that the procedure is quite simple, uses affordable materials and it seems not-too dangerous.
Before continuing, we should clarify that we only have basic skills on chemistry. The little we learned was when we where kids using a Cheminova toy and later at high-school. But Internet is a fantastic way to expand knowledge and if you have a basic level for understanding what you are reading you can learn many things.
So we bought 1kg of copper sulphate and 1Kg of ascorbic acid (in total we spent about €25) and we started to brew copper nanoparticles at our garage. Acid ascorbic, despite the name, is not so acid: it is simple vitamin-C.
We quickly adapted an old burnt-blender to make the mixes. We used a tin of baby milk powder to accommodate the motor. We call it the "LactoMix" in homage to the Thermomix©.
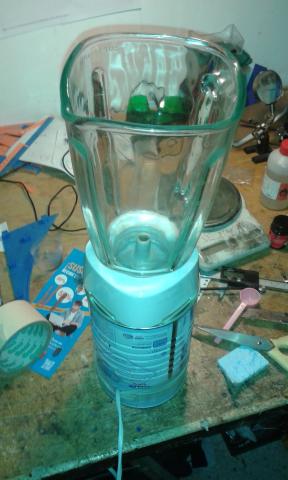
But we just got less than a gram.
We even tried using an ultrasonic capsule to see if we improved production, but no way.
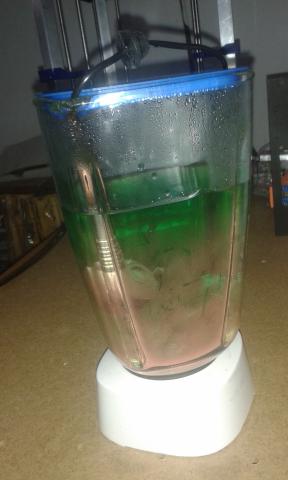
The resistivity of the final product is about 2-3Ohm per cm. We believe that it could be acceptable, at least for making vias.
We tried brewing 20 litters in a bigger container, just to pay off the Vitamin-C investment and see what happens.
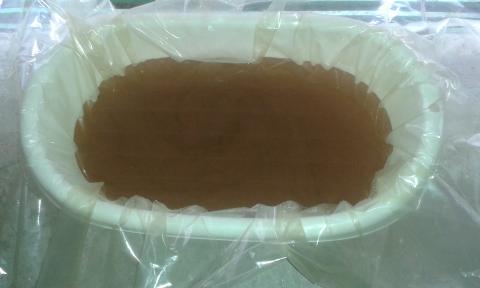
And after mining the solution we just got a few milliliters more. Not too much really. Finally we put the result into an empty Apiretal bottle and kept it in the safe box. :-)
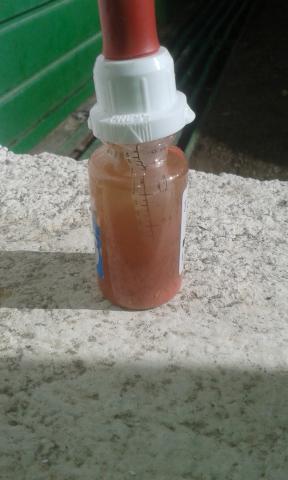
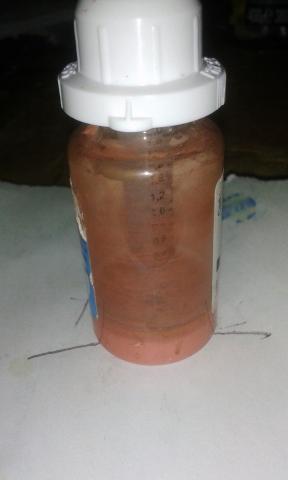
We are going to use it for "nano-testing".
Although production is easy and cheap, the method is not very productive so it does not meet our requirements.
We need a productive and cheap source of high-conductivity copper nanoparticles. We found it on the market but at “laboratory prices” aka prohibitive. In addition, the copper oxidizes very quickly and is difficult to find it in its pure form, since usually it is already covered by a thin film of copper oxide.
Interestingly, the copper oxide is cheap and we found it on ebay. It costs about €30 per Kg, but it is a poor conductor of electricity. Probably for this reason is so cheap.
Reading some publications on copper nanoparticles we discovered that there are ways to convert it into metallic copper (Cu) using a reduction reaction. It is a kind of reaction which the oxide loses the oxygen. This process is just the opposite of oxidation and is what we need if we want to use copper oxide.
To force the reduction we have to add energy and it can be done through heat (annealing), through chemical combination with other compounds, by light-flashing (using a powerful halogen lamp), by laser, and finally using some combinations of all of them.
It can be combined with hydrogen, carbon monoxide and nitrogen with the following results.
CuO H2 → Cu H2O
CuO CO → Cu CO2
CuO N2 → Cu N2O2
But the method we like is using the laser. We know a little about lasers and we have easy access to laser diodes. In addition, laser is a selective way of inducing the reaction. Perhaps we can make some kind of Cu oxide reactive paste sensible to UV light.
We could apply it with the Paste Dispenser ToolHead into the vias and then force the reaction with the laser and convert the oxide copper in metallic copper. Another option would be to use the IR laser and induce the reduction through heat. And another one, use a small cover on the via to inject some drops of liquid nitrogen and then hit the via with the laser on a N2 atmosphere.
Any of them has some kind of viability on a DIY environment and meets the criteria of cost.
So, we order 100gr of copper oxide (II) to test.
While we wait to receive it we must learn more about alchemy and spend the copper nanoparticles that we already brewed.
Anyway, I think we need some chemistry technical advice.
If any of you is chemist or is studying chemistry, has some knowledge about this topic and are interested on it please, contact us. Sure we can collaborate and make something useful for the DIY community.